R. Stephen Spinazzola, PE, LEED AP
Shumate Engineering, PLLC
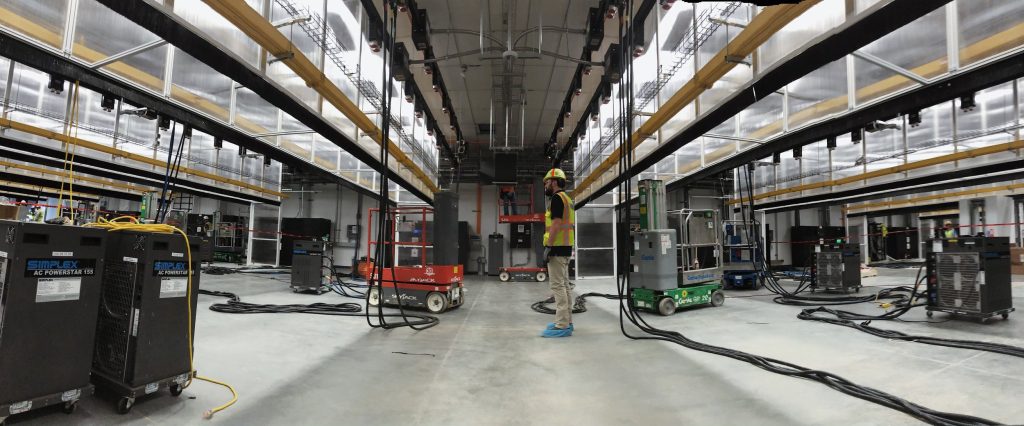
Adiabatic cooling, the reduction in temperature when air pressure is lowered, is well known to all, and is witnessed in nature. For instance, stand near a waterfall on a hot day and experience a refreshing drop in temperature- that’s adiabatic cooling. A warm air mass ascending a mountainside loses temperature as it rises- pilots and mountain climbers know that air is always cooler the higher you climb. Harnessing this same natural phenomena, commercial cooling towers systems are the heat of large-scale air conditioning system. This paper will explore adiabatic cooling in data centers; its use in cooling and economizer cycles; design and control considerations; and comparisons with chiller assisted cooling (CAC) and indirect/direct adiabatic cooling. We will present several design approaches that maximize adiabatic cooling for enhanced data center energy efficiency.
Adiabatic Cooling–The Basics
Adiabatic cooling is the process of reducing heat through a change in air pressure caused by volume expansion of a fluid resulting in “work” on the process water known as condenser water. The most common example in building cooling systems- the evaporation of water in a cooling tower- is adiabatic cooling.
Again, for data centers the most common use of adiabatic cooling is with cooling towers. A cooling tower rejects heat to the atmosphere through the evaporation of condenser water. The adiabatic process of evaporation cools the water that remains after the evaporation. (Figure 1).
Condenser water enters the top of the tower distribution grid as hot water and flows down through the “fill”, usually sheets of PVC designed to slow the water flow as the tower fans draw air up in a counterflow figuration. Air is induced by fans that move to cool dry air through the fill and evaporate approximate 1% of the water. This evaporation results in an approximate 10° F reduction in the condenser water temperature. The change in temperature or ΔT gauges the amount of cooling the adiabatic system produces.
As water evaporates, the concentration of total dissolved solids (TDS) increases. It is critical for an efficient adiabatic process that the TDS be controlled. To keep the condenser water from building up dissolved solids which can collect on the cooling tower fill, approximately 1% of the condenser water is “drained” through a bleed line to drain. The result is a consistent condenser water “turnover” of approximately 2% of the cooling tower flow rate of approximately 2 GPM per Ton of cooling. A data center cooling system use cooling towers to reject the heat from the chillers and have another cooling tower with a heat exchanger in parallel to the chillers as illustrated in figure 3.Traditionally, cooling towers were designed to provide an approximately 10°F ΔT at peak outdoor wet bulb design conditions for the geographic location of the building. For example, the design wet bulb temperature in Ashburn, VA is 78°F. Since a cooling tower is an adiabatic cooling device, it is not affected by dry-bulb temperature.
Figure 1 – Adiabatic Process in Cooling Tower – Graphic courtesy of Evapco
Legacy Chilled Water Plant with Economizer Cycle Utilizing Fluid Cooler
The traditional design of a chiller plant includes a chiller or chillers using a cooling tower or towers for primary heat rejection of the chilled water. A fluid cooler which is a closed loop cooling tower where the chilled water flows through a coil, and the condenser water is an open loop like a cooling tower. This is used to condition the chilled water while in economizer mode (no mechanical refrigeration) and in parallel with the chilled water plant.
The heart of the traditional design was the use of either the chiller or fluid cooler. This design is a proven approach that has been used for data centers and other types of buildings for well over 40 years. During that time, particularly in the last 10 years, the allowable temperatures in the data center space have been increased significantly with resulting significant impact on the cooling system. Supplying air at 75°F and returning air at 103°F has become the standard in the industry. With that in mind, this solution will provide many hours of “free cooling”, or as previously defined, economizer mode, when outside atmospheric conditions can be directly used as the cooling source.
While not as cost competitive on life cycle cost as a “Chiller Assisted Cooling (CAC)”, a chilled water plant in parallel with a fluid cooler offers a tried-and-true method of economizer where the need for lower chilled water temperatures do not allow for a series configuration.
Outside air (OA) is induced into the counter-flow fill to pre-cool the water that flows over the closed loop chilled water coil (Figure 2). This provides the benefit of pre-cooling the open loop condenser water before it cools the closed loop chilled water coil.

Design Examples of Chilled Water Plant with Economizer Cycle Utilizing Fluid Cooler
The following diagrams illustrate a solution for a prototypical 5 MVA IT load. The control scheme to switch from chiller operation to free cooling is important to ensure a constant chilled water flow rate and temperature.
Figure 3 shows the flow diagram in peak cooling load design conditions. This chilled water flow diagram illustrates chilled water flow with peak cooling requirements based on ASHRAE 4% design dry bulb and ASHRAE 4% non-coincident wet bulb. In this mode, the fluid cooler does approximately 33% of the cooling load, pre-cooling the chilled water where the chiller does approximately 67% of the cooling to maintain 68°F chilled water.
Figure 4 below illustrates the chilled water flow diagram with economizer mode in operation. In this mode, the fluid cooler cools 100% of the IT load bypassing the chiller plant.
Chiller Assisted Cooling (CAC)
While a typical data center with a chiller power plant operates at a respectable power utilization efficiency (PUE) between 1.3 and 1.5, the strategic insertion of an adiabatic cooler drives down the PUE significantly freeing up electricity for leasable IT load previously used for cooling. A drop in PUE from 1.3 to 1.2 on 5MVA results in 500 kW available to generate data center revenue.
CAC uses a fluid cooler to condition the chilled water in series with the chilled water plant. This design makes the evaporative cooling device the primary method of heat rejection. When wet bulb temperatures are 75°F or lower, the fluid cooler dissipates 100% of the IT load and produce 68°F chilled water. When the wet bulb temperatures are above 75°F the chilled water also flows through the chiller to maintain 68°F chilled water.
The use of a fluid cooler as the primary means of heat rejection of the chilled water allows for a reduction in the size of the chiller plant and emergency power plant that serves the HVAC equipment by approximately 33%. This also provides lower initial cost for the chiller plant and emergency power plant as well as fuel consumption during emergency operation. Initial reduced construction costs are also attributable to a reduction in pipe and insulation material and less copper for emergency power distribution.
This has significant potential to reduce construction budgets.
Figure 5 below illustrates the chilled water flow diagram with peak cooling requirements based on ASHRAE 4% design dry-bulb and ASHRAE 4% non-coincident wet-bulb. In this mode, the fluid cooler does approximately 33% of the cooling load, pre-cooling the chilled water where the chiller(s) do approximately 77% of the cooling to maintain 68°F chilled water.
The net result of having the fluid cooler in series with the chiller aside from the energy savings is the chiller plant is approximately 67% of IT load. An IT load of 1,422 tons only requires 910 tons of chiller plant. In addition, with the high leaving chilled water temperature at 68°F, the chillers operate at approximately 0.29 kW/Ton while having a Net Part Load Value (NPLV) of approximately 0.19 KW/Ton. This is an approximately 40% reduction in chiller operating cost.
Figure 6 below illustrates the chilled water flow diagram with economizer mode in operation. In this mode, the fluid cooler cools 100% of the IT load. The chiller plant is completely bypassed in this mode of operation leaving the energy hungry chillers idle.
Chiller Assisted Cooling w/ Adiabatic Cooling Package
Recognizing the benefits of CAC, manufacturers are producing solutions that specifically offer the energy efficiencies of CAC.
An engineered adiabatic cooling package with an adiabatic pad in series with the chilled water coil when the adiabatic cooling needs assistance from the chiller to maintain chilled water set point. The primary difference between the original CAC is this design uses a Hybrid Adiabatic/Dry Cooler.
With this design, there is an adiabatic pre-cooling pad in series with the dry cooling coil. The adiabatic pre-cooler evaporates 100% of the domestic supply water in the adiabatic media. There is no return line from the adiabatic pre-cooler and as a result, no sump.
This design uses up to 95% less water than a conventional cooling tower or fluid cooler. Reduction of water usage can become a critical design decision driver where water resources are limited and/or heavily regulated.
Figure 8 below illustrates the chilled water flow diagram with peak cooling requirements based on ASHRAE 4% design dry-bulb and ASHRAE 4% non-coincident wet-bulb. In this mode, the fluid cooler does approximately 33% of the cooling load, pre-cooling the chilled water where the chiller does approximately 67% of the cooling to maintain 68°F chilled water. This design shares the same savings in chiller sizes and material costs as the original CAC. With the use of a Hybrid Adiabatic/ Dry Cooler there is an approximately 95% reduction in the annual use of domestic water.
Again, the reduced water usage helps drive potential design decisions in evaluating potential cooling systems.
The following diagram, Figure 9 illustrates the chilled water flow diagram with economizer mode in operation. In this mode, the Hybrid Adiabatic/ Dry-cooler cools 100% of the IT load. The chiller plant is again, completely bypassed in this mode of operation.
100% OA Economizer w/ Supplemental Adiabatic, Chilled Water or Packaged DX Cooling
An engineered packaged cooling unit designed to primarily cool with outside air and utilize supplemental cooling as needed to maintain required space conditions. Supplemental cooling options include adiabatic, chilled water or packaged DX cooling. The units are designed to be installed outside of the data center and can be added modularly as the data center is expanded. Each unit includes a mixing box, filtration, supplemental cooling, supply & return fans with single point power and factory packaged controls.
Figure 10 – 100% OA Economizer with Supplemental Adiabatic, Chilled Water or DX Cooling. Graphic courtesy of Integra Mission Critical
Summary
Many factors must be considered in formulating a cooling approach to data centers such as geography, weather, climate, power costs, availability of make-up water, data center operations approach, and many others. Driving down PUE is always a goal in data center design and creative application of adiabatic offers to chilled water plants offers viable solutions to accomplish this goal.
CAC with a Hybrid Adiabatic/ Dry Coolerand 100% OA (with a mixing box) with indirect adiabatic and direct adiabatic cooling in series are the most efficient system in this example.
This paper illustrates the progression in adiabatic cooling technology over the last 40 years. The increase in allowable supply air temperatures and hot aisle containment has created the opportunity for CAC with a Hybrid Adiabatic/Dry Cooler, and 100% OA With Indirect Adiatabtic and Direct Adiabatic Cooling in Series to become cost effective, especially with taking into account the total cost of ownership.
REFERENCES
Rabe, C., Gaston, D., Lewis, M., Mohr, D., Rotheroe, D., Kelley, D., Wilcox, E., Wessels, K., Fitch, J., Dutra, A., Collins, J.,. Hollingsworth, M., Wheeler, S., Fischer, P., Bean, J., Avelar, V., Taylor, J., Cram, M., Faulkner, R., Prisco, J., Schmidt, R., Brodsky, W., Estilow, P. (2016) ASHRAE TC9.9, Data Center Power Equipment Thermal Guidelines and Best Practices. Available at: https://tc0909.ashraetcs.org/documents/ASHRAE_TC0909_Power_White_Paper_22_June_2016_REVISED.pdf, Accessed 04/June/2018.
Spinazzola, R. et al. (2002, 2003, 2004) Computer Room Heat Extraction Device, 6,412,292, 6,494,050, 6,557,357, 6,722,151, 6,745,579.
Design developed while at CRTKL, September 18, 2012 – September 25, 2014.
NOTES
The weather data used in this study was for Ashburn, VA.